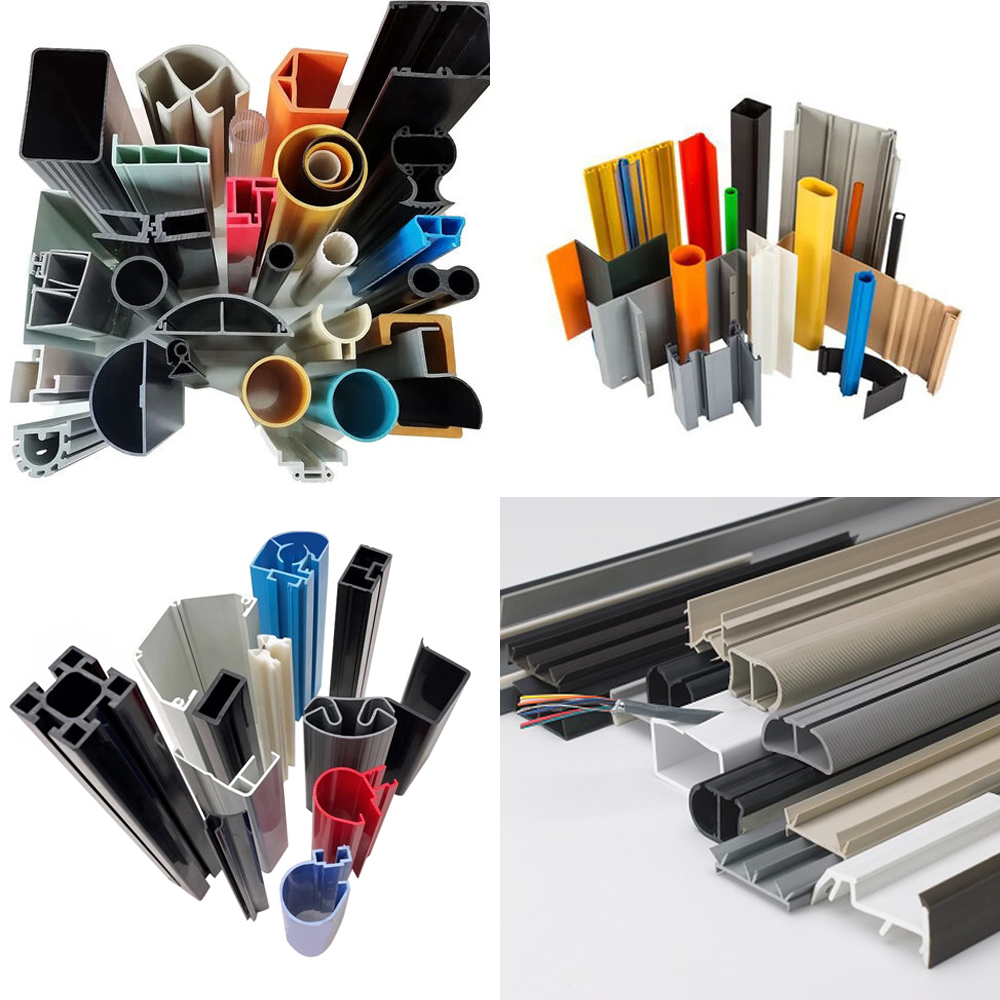
Profile Extrusion
Profile Extrusion:
What is Profile Extrusion:
Profile extrusion is the process of creating continuous shapes of plastic through extrusion. The plastic products produced by profile extrusion can be solid (like vinyl siding) or hollow (like drinking straws).
The profile extrusion process resembles the process of other extrusion methods up until the die is introduced. First, raw plastic materials are fed into a hopper and extruder. A rotating screw keeps the plastic resin moving through the heated barrel, which is set to the material’s specific melting temperature. Once the resin is melted, mixed, and filtered, the plastic will be fed into the extrusion die. The die will be placed in cool water to solidify the product. Finally, the die will be moved to the take-off rollers, where the final product is removed from the die.
A pin or mandrel must be placed in the die to make hollow shapes. Then, air should be sent through the center of the product via the pin to ensure the final product maintains its hollow form.
Applications of Profile Extrusion Process:
The profile extrusion process was invented to produce items of varying shapes easily. Today, this method is used in a wide range of applications, including in the production of medical packaging and residential construction products. Here are just a few of the products made with profile extrusion:
- Piping
- Recreational products
- Tubing
- Water and wastewater
- Sealing sections
- Edging
- Office
- Marine
- Window profiles
- Moldings
- Decorative trim
- Cooler bumpers
- Modular drawer profiles
- Telecommunications
- Irrigation
- Janitorial
- Medical
- Plastic Fencing
Benefits from Profile Extrusion:
Whether it’s hundreds of yards of tubing or thousands, profile extrusion is one of the leading ways to produce plastic parts. It offers a range of advantages, which include:
- High production throughput
- Low tooling costs
- Inexpensive process
- Product combinations possible
- Design freedom
The profile extrusion process is incredibly versatile. Operators can create products with complex shapes of varying thicknesses, strengths, sizes, colors, and textures. Additionally, additives make it possible to improve the performance characteristics, such as durability, fire resistance, and anti-friction or static properties.
Materials for Profile Extrusion:
Our materials can be matched to virtually any color imaginable. Some materials are matched in-house by our own color experts, and others are matched through relationships with our world-class pigment and colorant partners.
Our extruded plastic parts are used in the automotive, processing, medical device, construction, marine, RV, and household appliance industries. Some of the materials available are:
- PETG (polyethylene terephthalate)
- Noryl® PPO
- Polyethylene (HDPE, MDPE, & LDPE)
- Polypropylene
- EHMW (extra-high molecular weight polyethylene)
- TPO (thermoplastic olefin)
- TPV (thermoplastic vulcanizates)
- TPU (thermoplastic polyurethane)
- Custom compounds
At Preferred Plastics, a key component of our turnkey extrusion and finishing services is our dedicated customer support from your initial call through delivery of the finished product. We work with you to ensure that your part’s tooling and engineering is accurate before manufacturing begins.